
Wham Bam XTR Flex Plate Anycubic Photon M3 Max
0
41
0
The Plate
I’ve been using and testing the Wham Bam XTR Flex Plate system on my Anycubic M3 Max for over a year now, and it’s been an absolute game-changer. Prints peel right off every time without struggle. The magnets are super strong, and I’ve seen no layer shifting or other print artifacts during its use. This magnetic build plate has handled it all like a champ even when printing large or flat models. Let's walk you through how to install this magnetic build plate on your printer. Installing this flex plate system is pretty straightforward, but before we start you will need to print a spacer and buy some screws.
Z-Axis Spacer

Due to the extra thick nature of this magnet, the build plate does not have enough extra space to account for the additional millimeters, so we’ll need to offset the sensor arm that tells the printer when it has reached the bottom. This spacer makes the arm trip the sensor earlier to account for the added thickness. Wham Bam provides the file needed for each printer. (https://www.thingiverse.com/thing:5407682). Print the 3.8mm spacer in either resin or PLA. To hold this spacer in place, we’ll need to buy some M3 screws that are 10mm in length to replace the 5mm screws that currently hold the sensor arm. (My local hardware store has a super organized screws section so finding what I needed was very quick and easy) With these new screws and spacer, we will be able to install and level our new magnetic build plate extension safely.
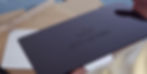
Magnet Install
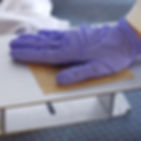
Clean and sand the old metal build plate surface with the included 220 Grit sandpaper. Try to smooth out any cuts, bumps, or divots to create a flat-level surface for our adhesive to bond to. Make sure the build plate is completely clean after sanding and wear a mask to prevent the inhalation of any fine metal particles.
Practice squaring up the magnet before removing the adhesive protection to get an idea of how the final fit should look. Try not to touch the clean buildplate surface with your bare hands. Body oils or other residue may reduce the bond between the sanded metal surface and the adhesive.

Once you’re ready, peel about 2 inches of the 3M adhesive protection paper
Square up the exposed adhesive edge to the build plate and press it down
Slowly peel the paper an inch at a time while pressing out from the center to avoid any air bubbles.
DO NOT CUT THE MAGNET - I was informed by the Wham Bam CEO that this step is not recommended. In my video, I show the magnet being cut to form, but this exposes untreated parts of the magnet to the harsh chemicals found in resin and cleaners. The magnets come with a protective coating to prevent wear due to chemical exposure. While I have not seen any issues with my magnets over the past year, it's probably better to avoid cutting into the magnet directly.
Now that your magnet is securely attached, let it sit undisturbed for 72 hours. This is necessary to ensure a strong bond is formed between the magnet and the old buildplate surface.

While we wait, we can touch up one side of the flexible buildplate surface with the included 400 Grit fine-grain sandpaper. This will increase the first-layer adhesion of your prints since the slick smooth surface is not always ideal for printing. Keep one side smooth. This will be the side that will face the magnet so we want to keep it unscuffed.

After waiting the proper 72 hours, we can now place the flexible build plate onto the magnet
I find the best way to line this up is to place the build plate edge on your table and use the table to guide the bottom edge of the metal plate to line up with the magnet before allowing it to smack back to the magnetic surface
Once everything is aligned, the last step is to level the build plate. Click here to check out my quick 5-step tutorial on how to level your build plate on the M3 Max.
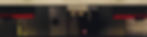
Make sure you’ve installed your Z-Offset spacer before beginning this process to prevent damage to the screen or motor.
And you're done! You now have a fully functional build plate with a magnetic build surface!
Cleaning
Make sure not to leave the magnet sitting in resin or isopropanol for long periods of time and make sure to clean it thoroughly after every print. Any trapped resin between the flexible build surface and the magnet could degrade the magnetic surface or adhesive bond over time.

Final Thoughts
Overall I think this system would be a huge benefit to anyone utilizing this printer. There’s nothing more frustrating than to damage a near-perfect print during its removal from the build plate. This system seems reliable and effective for almost every application I’ve tested. Being able to pop off prints without placing my full body weight on a metal scraper to try and get an edge under my resin print is worth every penny, and so far this specific XTR system seems more than capable of handing the prints I’ve thrown at it. While it's generally best practice to avoid printing objects directly on the build plate with no raft or supports, there have been times when I've needed to do just that. Having a flexible build plate meant I was able to remove the print easily from the plate without damage.
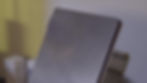
Update: 1 Year Later
After using this flexible build plate system across three different M3 Max 3D resin printers for over a year now, I have come to some interesting new conclusions. The flexplate system works great, and as a build surface, is really smooth and reliable, but I find myself not being able to take full advantage of the flexplate's key feature. Most of the time, prints are either too small or too flexible to come off the plate by just simply flexing the plate. More often than not, I end up needing to re-attach the plate to the magnet & use the spatula to pop prints off the old-fashioned way. Don't get me wrong, having the option to remove the plate has its benefits & there are plenty of times, especially with larger prints, that the flexplate helps to either pop the whole print off the plate or sometimes it will cause the supports to pull away from the model enough to remove the finished model for cleaning.
